1. Why performing regular maintenance is important?
Performing regular maintenance is crucial for several reasons:
Prevent Equipment Failure: Regular maintenance helps identify potential issues before they become major problems, preventing costly breakdowns and downtime.
Extend Equipment Lifespan: Proper maintenance can prolong the lifespan of machinery and equipment by keeping them in optimal condition, reducing the need for premature replacements.
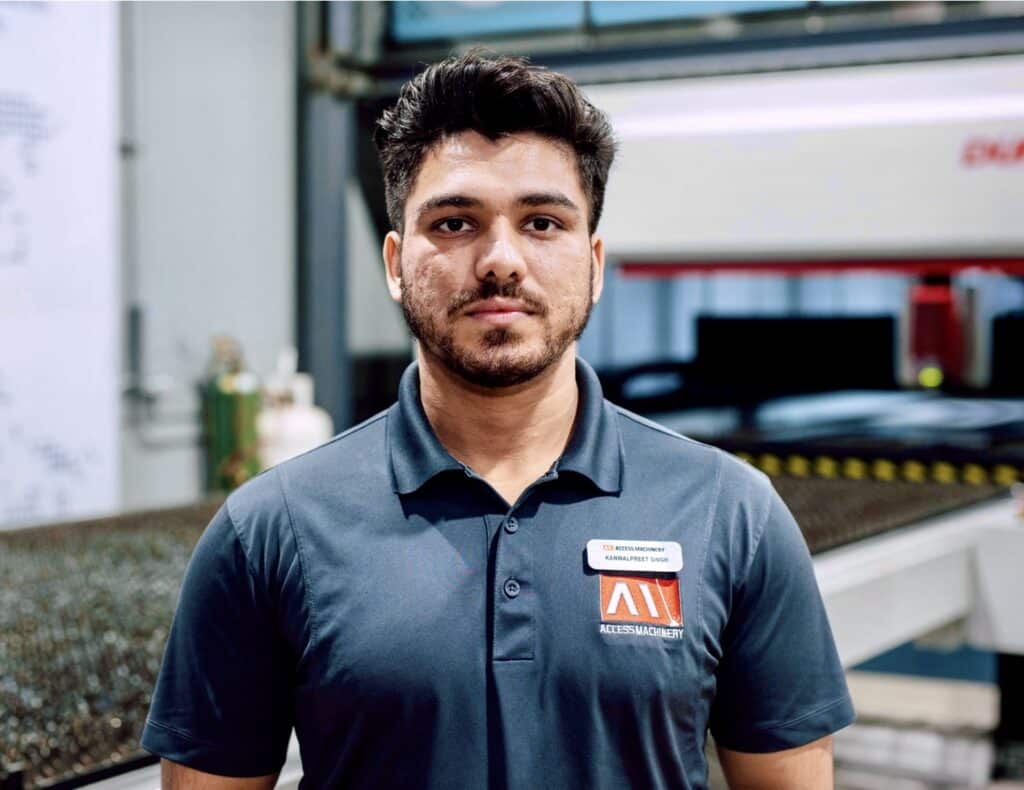
Ensure Safety: Regular inspections and maintenance procedures help ensure that equipment operates safely, reducing the risk of accidents and injuries in the workplace.
Maintain Efficiency: Well-maintained equipment operates more efficiently, which can lead to increased productivity and lower energy consumption.
Compliance with Regulations: In many industries, regular maintenance is required by law or industry regulations to ensure safety and environmental compliance.
2. How much money and downtime the regular maintenance will save and prevent?
Investing in regular maintenance, businesses can reap substantial financial savings, minimize downtime, and ensure the long-term reliability and efficiency of their equipment.
The financial and downtime savings from regular maintenance is significant as customers can prevent unexpected costly repairs and downtime with proactive maintenance strategies.
For instance, machine part’s damage due to poor maintenance requires costly replacement and technician visit could cause drastic burden on the business that could be avoided given the proper maintenance was performed at right intervals. Over the time following regular maintenance schedule let the business and production run smoothly with minimal to zero downtime and money invested.
3. How much lifetime on machine parts regular maintenance will prolong?
Regular machine maintenance frequency and the quality of maintenance performed can also significantly prolong the lifetime of machine parts. While it’s challenging to provide a precise percentage, proper maintenance can often extend the lifespan of machine parts by 20% to 50% or more, depending on the maintenance practices.
For instance, lubricating moving mechanical parts to minimize the friction between them reduce the mechanical wear and tear dramatically.
4. Who should be doing it? Who should be controlling it?
Maintenance tasks should only be performed by trained technicians or maintenance personnel within the organization. It’s essential to have clear protocols and schedules for maintenance tasks, with designated personnel responsible for carrying them out. Additionally, maintenance activities should be overseen and controlled by supervisors or managers to ensure that they are completed correctly and on time.
5. Example on regular maintenance on fiber laser and the brake that equipment owner should do.
Laser maintenance
- Consumables (Inspect the nozzle alignment and consumables as some aftermarket suppliers can reverse engineer an OEM part which results in replacing the consumables that are out of specifications which lead to bad cuts or potential cutting head crash that incurs extra repair costs.
- Check lenses and mirrors for any signs of damage, dirt, or degradation. Clean or replace as necessary to maintain optimal cutting quality.
- Cleaning and lubricating moving mechanical assemblies.
- Verify that the gas supply (e.g., oxygen, nitrogen) is adequate and at the correct pressure for cutting operations. Replace gas cylinders as needed.
- Monitor and record laser power output to detect any fluctuations or deviations from the specified range.
- Check the water level and temperature in the machine’s cooling system. Ensure that the water is circulating properly to prevent overheating of laser components.
- Wash/clean filters for dust extraction system.
Press Brake maintenance
- Required lubrication after specific number of strokes as per manufacturer recommendation.
- Check hydraulic hoses, fittings, and seals for leaks, wear, or damage. Test hydraulic pressure and adjust as needed to maintain consistent bending performance.
- Verify the accuracy of the back gauge by measuring distances between the back gauge fingers and the bending point. Adjust settings if necessary to ensure precise positioning of the workpiece.
- Check hydraulic fluid level and condition in the reservoir. Replace or replenish hydraulic fluid as needed and inspect filters for clogs or contamination. Flush and refill the hydraulic system according to the manufacturer’s recommendations.
- Check the condition of bending tools, including punches and dies, for signs of wear, damage, or misalignment.
6. Why we recommend preventative maintenance visit once a year?
At Access Machinery, we always encourage our customers to follow and complete periodic maintenance schedule. We provide customers with the maintenance journal that helps them track the machine maintenance periodically.
Preventative maintenance is recommended once a year to catch any potential issues early and ensure that equipment remains in optimal condition. By conducting regular inspections and maintenance tasks annually, customers can minimize the risk of unexpected breakdowns and maintain the efficiency and reliability of their equipment.
7. What are the benefits for customers?
The benefits of preventative maintenance for customers include:
Reduced Downtime: By preventing unexpected breakdowns, customers can minimize costly downtime and maintain productivity.
Cost Savings: Preventative maintenance helps avoid expensive repairs and replacements, saving customers money in the long run.
Improved Safety: Regular maintenance ensures that equipment operates safely, reducing the risk of accidents and injuries for operators and other personnel working around the machines.
Extended Equipment Lifespan: By keeping equipment in optimal condition, preventative maintenance can prolong its lifespan, allowing customers to maximize their investment.
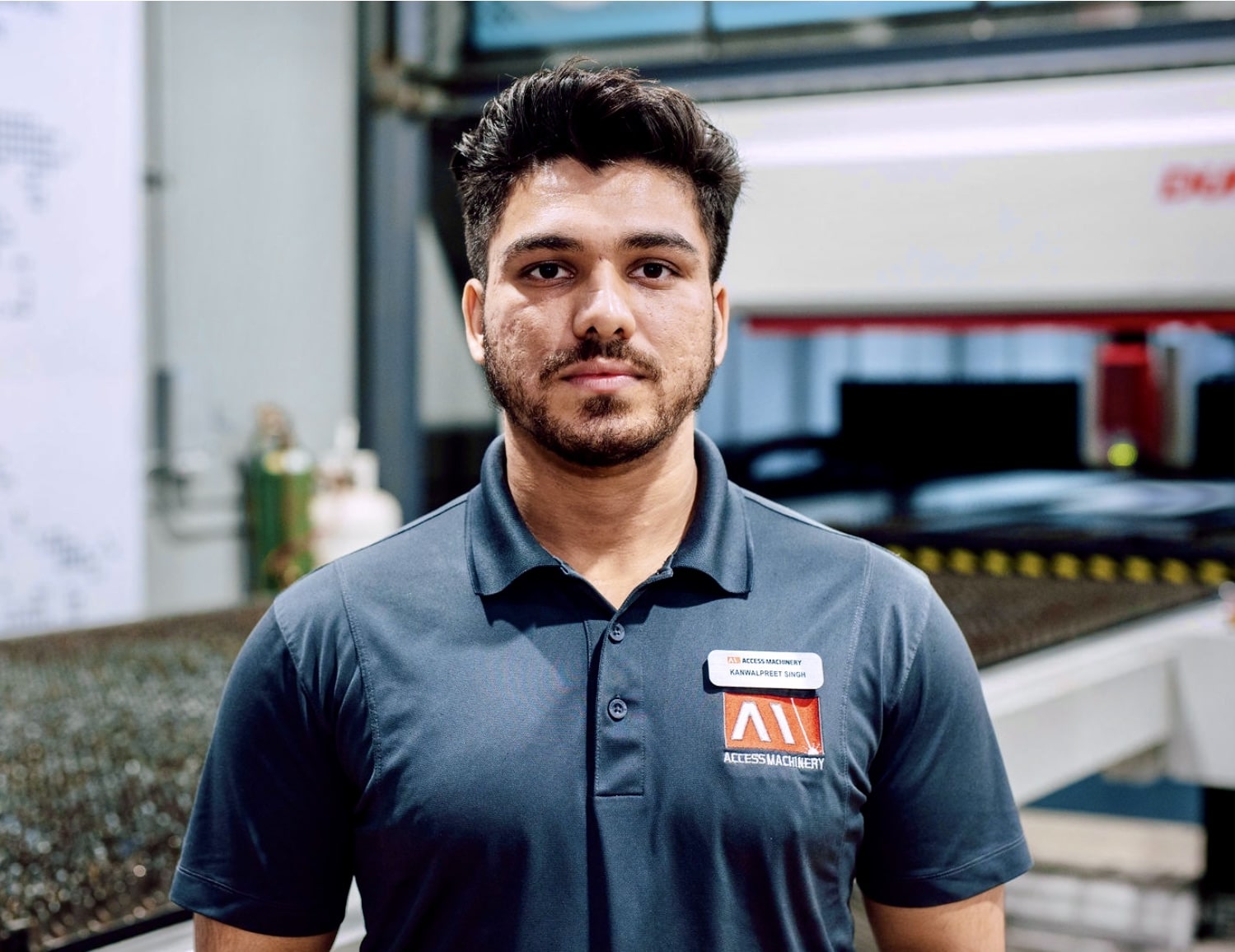